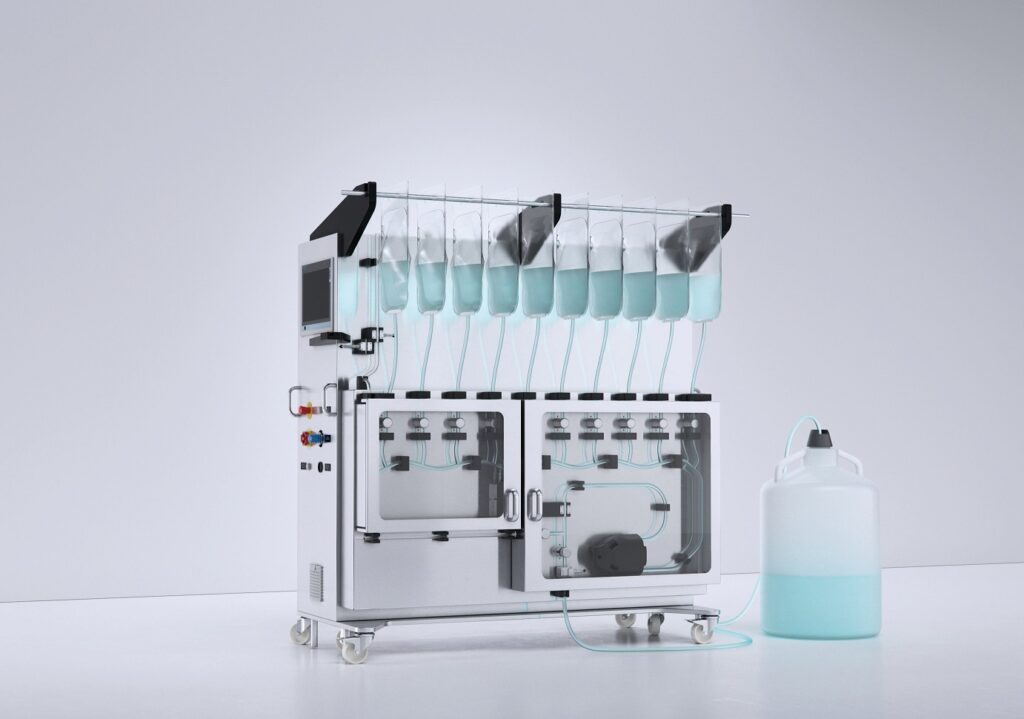
Automation of Adherent Cell Cultures for a Leading Vaccine Manufacturer
Automation of Adherent Cell Cultures for a Leading Vaccine Manufacturer
Context
In the field of vaccine production, one of our leading biopharmaceutical clients faced the need to enhance the efficiency and traceability of their adherent cell culture processes. This challenge was addressed by integrating our tailored automation solution for adherent cell cultures, specifically designed to meet the stringent requirements of controlled environment production areas (ZAC).
Solution
We implemented a comprehensive automation solution for adherent cell cultures, incorporating multi-layered cell culture systems such as Cell Factory™ and Cell Stacks™. This solution is based on an optimized combination of automated equipment, including:
- Robotic manipulators
- Robotic shakers
- Rack transfer elevators for MT40 or CF40
- Combined with Automated fluid transfer systems
This infrastructure enables the automated management of all critical stages of the cell culture process:
- Automated mechanical movements: Such as rocking, shaking, filling, balancing, and draining positions
- Automated fluid transfers: Including seeding, inoculation, media transfers, washing and rinsing phases, trypsinization, and harvesting
The interconnection of equipment through a recipe management platform ensures strict adherence to production processes, guaranteeing high repeatability and complete traceability in compliance with cGMP standards and 21 CFR Part 11.
Results
Thanks to this scalable and adaptable solution, our client significantly increased their production yields while maintaining strict control over the quality of the final products. The systems implemented allowed the simultaneous handling of up to 6 CF40 or MT40 racks, with perfectly regulated fluid transfers, offering complete traceability at every stage of the culture cycle (batch records and audit trails management).
Moreover, the solution integrates seamlessly with existing infrastructures, meeting the highest standards (Grade B / ISO Class 5) and ensuring full compliance with current regulations.
Conclusion
The integration of our adherent cell culture automation solution not only enabled our client to meet their production objectives but also enhanced the reliability and safety of their processes. This case study highlights our ability to deliver innovative and customized solutions tailored to the specific needs of biopharmaceutical leaders.
Benefits
Benefits of Our Adherent Cell Culture Automation Solution:
- Simultaneous handling of up to 6 CF40 or MT40 racks
- Fluid transfers regulated by peristaltic pumps and pinch valves
- Pre-programmed recipes for complete manipulation cycles
- Complete traceability of racks or stacks throughout the cycle
- Easy handling for incubator entry and exit
- Compliance with cGMP guidelines & 21 CFR Part 11
- Grade B / ISO Class 5 for superior quality
- Integration into existing production areas
Configurations
Technical Specifications
Elements | Processing range |
---|---|
Circuit Type | Single Use System |
Cell Culture Type | Adherent Cell Culture in Cell Stacks™ |
Shaking Table |
|