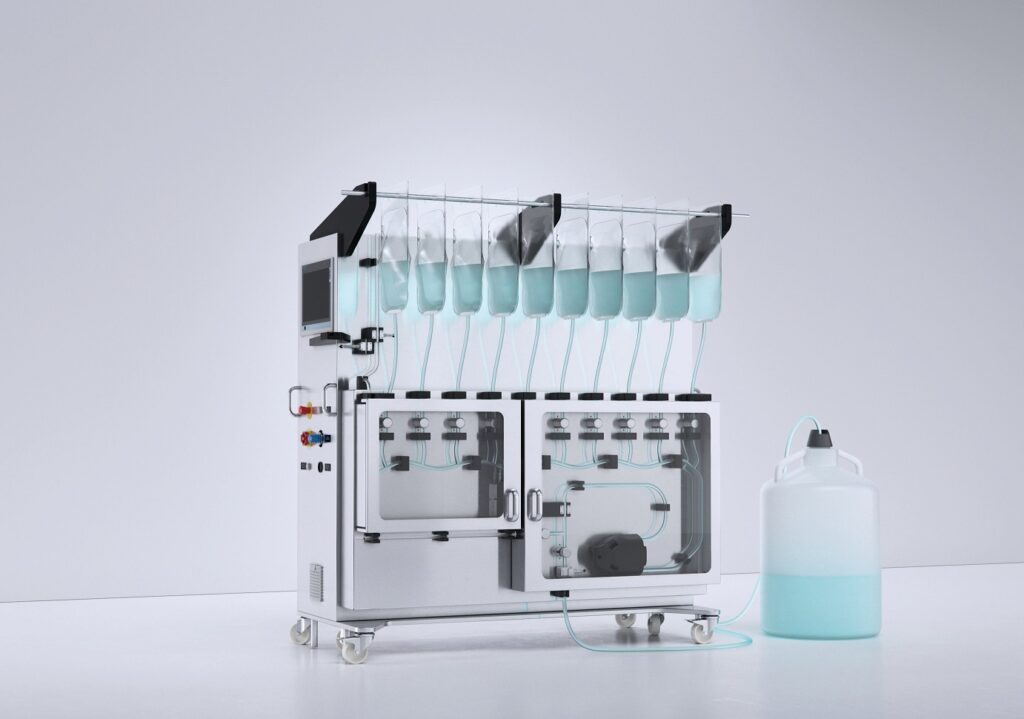
Automated Bioprocessing Solution with PUPSIT for Sterilizing Filtration in Biotech Industry
Automated Bioprocessing Solution with PUPSIT for Sterilizing Filtration in Biotech Industry
Maximize safety with automated sterilizing filtration. Integrated PUPSIT ensures integrity before and after sterilization.In the highly regulated biotechnology sector, automating production processes is essential to ensure the quality and safety of pharmaceutical products. One of the major challenges faced by biotechnology researchers and production managers is to ensure product sterility while optimizing process efficiency. Our solution stands out as a state-of-the-art bioprocessing automation system, specifically designed to meet the stringent needs of the Big Pharma sector.
Solution Overview
Our advanced bioprocessing automation technology is dedicated to the sterilizing filtration of vaccines and parenteral drugs before the filling stage. This system integrates critical features such as PUPSIT (Pre-Use, Post-Sterilization Integrity Testing), thereby guaranteeing filter sterility and integrity at every production cycle. With its compatibility with single-use systems, our solution easily interfaces with various integrity testing equipment and is adaptable to a wide range of sterilizing filters available on the market.
The system automates the transfer and final filtration of products, efficiently linking the finished product vessel to the filling machine. Its modular design allows seamless integration into different production environments while complying with the strict requirements of cGMP and GAMP5. Additionally, its compatibility with stainless steel piping technology and sterilizing filtration capabilities make this system a preferred solution for downstream bioprocessing.
Competitive Advantages
This solution offers several competitive advantages for pharmaceutical industries:
- Strict Compliance: The system is fully compliant with GMP Annex 1, ensuring adherence to the highest standards of sterility and quality.
- Flexible Integration: It is designed to accommodate various filter sizes and brands, allowing maximum flexibility in configuring single-use assemblies.
- Space Optimization: With its compact design, the system requires minimal floor space, optimizing production area utilization.
- Precise Regulation and Monitoring: Flow regulation and real-time monitoring ensure optimal management of filtration processes, minimizing the risks of errors and contamination.
- Data Traceability and Integrity: The system enables automated production data reporting to the client’s SCADA, including batch reports and audit trails, ensuring complete traceability and data integrity.
Technical Features
Elements | Processing range |
---|---|
Application |
|
Filters |
|
Flow Rate | Adjustable to filling equipment requirements |
Dimensions | Customizable, with a minimum footprint of 850 x 1000 x 1975 mm |
Frame |
|
Electricity |
|
Interface | 15″ or 17″ Touchscreen |
Standard Integrity Testing Equipment |
|
Integration |
|
Data Monitoring |
|
Certification |
|